Is there any downside to these at all? Everything I have read about them implies only good things, although the only cars I see with these (with the exception of some supercharged ones) are street/strip and drag only monsters. Water has one of the highest specific heats which makes it great for "absorbing" heat from air. I guess I just don't get why anyone would choose a FMIC over these.
Do they require a separate water pump to supply enough pressure or is it that the stock radiator just isn't efficient enough for them to be effective on our cars. The reason I ask, is because I have an idea for where to put it with a top mount ramhorn (when I eventually get around to turboing this bitch).
-
"Youth in Asia"...I don't see anything wrong with that.
I have yet to find a down side to this. nobody wants to do it, becuase its different, and anything thats not compleatly worn out doesnt really fly here. your going to need anther pump by the way. but there easy.
"
Kick azz is my boost hero!!! 
"
I'm working on one for my DSM. Downsides are added weight from all the water, the need for another pump, a circuit to tell it when to come on (depending on the pump type you will need completely different circuits), a seperate heat exchanger (2nd radiator type unit, I'm using a stock 2g RX7 oil cooler), extra bracketry and hosing for the 2nd heat exchanger (which adds significant weight in itself), and some people have a seperate reservoir to feed the system (so you can add ice). DO NOT use the same fluid that is running from through your engine coolant system (it won't cool nearly enough), run a completely seperate water system. Also, air/water exchangers tend to be more expensive for just the main unit.
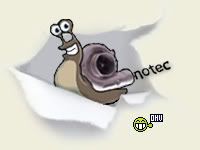
fortune cookie say:
better a delay than a disaster.
Yea I've always heard "dont do this on a daily driver, blah blah blah" but never a good reason as to why either. This is something I've always been interested in
Listening.
it is much more effecient, and if you do it... you are kinda a big deal.. people know you. ( I am drinking)
do you have many leather bound books??
HP Tuners | Garrett T3/T04B | 2.5" Charge Pipes | 2.5" Downpipe | 650 Injectors | HO Manifold | Addco front/rear | Motor Mounts | HKS SSQV | Spec stage 3 | AEM UEGO Wideband | Team Green LSD | FMIC | 2.3 cams | 2.3 oil pump swap | 280WHP | Now ECOTECED
OHV notec wrote:I'm working on one for my DSM. Downsides are added weight from all the water, the need for another pump, a circuit to tell it when to come on (depending on the pump type you will need completely different circuits), a seperate heat exchanger (2nd radiator type unit, I'm using a stock 2g RX7 oil cooler), extra bracketry and hosing for the 2nd heat exchanger (which adds significant weight in itself), and some people have a seperate reservoir to feed the system (so you can add ice). DO NOT use the same fluid that is running from through your engine coolant system (it won't cool nearly enough), run a completely seperate water system. Also, air/water exchangers tend to be more expensive for just the main unit.
Just a suggestion but you might want to look for an Audi Rad for your heat exchanger. I ran one on my water to air last year and temps dropped quite a bit and best of all they are cheap.
Water to air is the most effective way to cool the intake air charge but they are a lot more complicated and more expensive to setup which is why you mainly only see them on track cars. One of the best setups I have seen for the track is to run your coolant lines in through the passangers side of the firewall. On the floor on the passangers side you put a nice big family sized beach cooler. Then take your heat exchanger and drop it into the cooler. You will have to drill and seal some holes in the cooler to allow for your coolant lines to pass though. Then you can fill the cooler up with ICE and your heat exhanger is now submirged in ICE and will allow for the best possible cooling. Obviously this setup is for a track car but with some quick connects at the firewall you can still run a front mount heat exchanger on the street. It would just be a matter of disconnecting your hoses from your front mounted heat exchanger and plugging them into the firewall when your at the track. I was going to run this setup last year with mine but plans changed.

I still might do it later on down the road but it's just not in the budget this year.
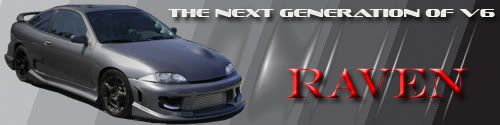
Quoth the Raven 'Nevermore
raven@accesswave.ca
Raven Autosports
55 McQuade Lake Cres,
Halifax, Nova Scotia, Canada
(902) 850-3330
10.82@132
on the suggestion of a few differnt members, i picked up "maximum boost". this book is an awsome read. well in any case, i was reading through all of this the other day. an air/air intercooler will never allow you to exceed 100% efficiancy. never. the water/air cooler, like mentioned above, is more added weight, and more expensive, but the pressure loss from this system is far less than on an air/air system. thus allowing the benifits of the system to allow you to reach an efficiancy level above 100%.
So basically all that would be needed is
1) W-A intercooler and charge pipes
2) external electric or belt driven water pump and I/O water hoses
3) Engine oil cooler (and not necessarily a full blown engine radiator)
4) separate reservoir
Does that sound about right.
And...
OHV notec wrote:I'm working on one for my DSM. Downsides are added weight from all the water, the need for another pump, a circuit to tell it when to come on (depending on the pump type you will need completely different circuits), a seperate heat exchanger (2nd radiator type unit, I'm using a stock 2g RX7 oil cooler), extra bracketry and hosing for the 2nd heat exchanger (which adds significant weight in itself), and some people have a seperate reservoir to feed the system (so you can add ice). DO NOT use the same fluid that is running from through your engine coolant system (it won't cool nearly enough), run a completely seperate water system. Also, air/water exchangers tend to be more expensive for just the main unit.
Are you being redundant here or do you mean not to run a 40/60 mixture of coolant and water...and possibly straight water? I'm just a little confused about exactly what you meant
-
"Youth in Asia"...I don't see anything wrong with that.
do not run a straight water mixture. you need to run the same mixture as you would run in the engine. what he was refering to by the ice comment is, in some race applications, people run the hoses, through a box, or cooler that is sealed, and then they fill it with an ice/water mixture to help take the heat out of the water. now weather you go with an air/air or an air/water cooler, you can set up a "sprayer" somthing to keep in mind here, is if you use nitris, or another gas that freezes on contact, as soon as you have a layer of ice on the cooler, it then is insolating the hot air in the cooler...
^^^So you mean redundant. If you are using a seperate isolated reservoir and pump, you are already not using the same fluid that is running through the engine. I just wanted to be sure...thanks for the clarification Mike.
-
"Youth in Asia"...I don't see anything wrong with that.
think of it as to completely closed systems. the mixtures do not intermix, but at the same time they contain the same liquid. basically all that means is DO NOT tie into an existing water line for this, because the water will be so hot, it will not do anything anyway.
Thats basically what I said...but thanks again.
-
"Youth in Asia"...I don't see anything wrong with that.
Yeah, not the fluid coming from the motor. However, if you don't have to worry about below freezing temps (I don't), run straight water. Engine coolant has a lower specific heat, and won't cool the air as much.
This is a good read on the air/water setups, and mentions quite a bit about the pumps and circuits. (The pic on top of the article is exactly how I would run one on one of our LN2s

)
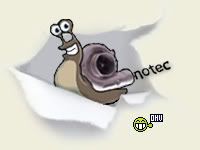
fortune cookie say:
better a delay than a disaster.
The best possible liquid for cooling would be distilled water mixed with Redline Water Wetter but like it was posted above only if you don't have to worry about freezing temps.
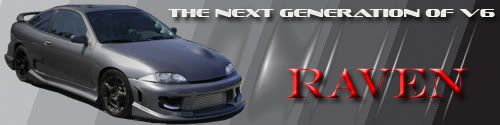
Quoth the Raven 'Nevermore
raven@accesswave.ca
Raven Autosports
55 McQuade Lake Cres,
Halifax, Nova Scotia, Canada
(902) 850-3330
10.82@132
I'm putting together another ecotec turbo kit.
I've really been thinking about using the Cobalt SS intake Manifold, for its intercooling capabilites. Would save a lot of charge pipe routing, and would def. be different.
The turbo swaps on the SS are putting down 90deg. IATs, so it def. works well. Even better, if you go with the dual pass intercooler plate. It would take a little extra time and money, but can very easily be done.
The only problem is mounting our TB to that intake manifold. Something that would have to be custom made.
For all us ecotec owners, its just there waiting. I'm really surprised nobody has done this yet.
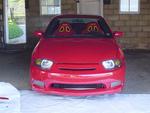
Hmmm....
Ok, so you've replaced your air to air cooler with an air to water cooler and you know it's a "cool" thing. You've got a separate coolant reservoir, temp activated pump, and the heat exchanger. And you're driving around town on a Saturday afternoon in July when it's nice and warm. Underhood temps are exceeding 200 deg F but you put the coolant reservoir in the trunk so no problems, right? But as you drive you notice on your datalogging laptop (you do drive with the laptop connected, right?) the IAT's are slowly climbing. Up, up, up they go until they're at least as high as underhood temps. You open the trunk to find that the coolant reservoir is hot to the touch and there's no way to cool it down without sitting and waiting or dumping the coolant and adding more. Sheesh... this sucks! At least with an air to air cooler you could get out where air movement across the cooler would bring temps back down. Back to the drawing board.
So you managed to get the air to water system redesigned so it's now an air to water to air cooler. You've added a second heat exchanger to remove all the heat energy that the water picks up through the first heat exchanger. You've added a temp controlled fan to go along with the temp controlled coolant pump. You put the second exchanger in the trunk to keep it away from engine heat. And you got it done before summer is over so you can go back out to test the new system. And sure enough, the new system keeps IAT's lower with the second cooler than without. How much cooler? Well, that depends on the efficiency of the first cooler, the efficiency of the second cooler, the volume of coolant pumped by the pump, the amount of air moved by the fan, and the difference in temperature between intake air, coolant, and ambient air. Regardless of efficiency though it's definitely cooler than air to water only. Now you happen to get to an area where you can open it up and you notice on the laptop that IAT's aren't dropping all that much. They're staying close to the level they were at when you were in town driving from one stoplight to another. You stop and open the hood and find that the engine compartment has cooled down some because you were moving pretty fast. But when you open the trunk the fan is running on the new heat exchanger and warm air is coming out the other side. The reservoir is also warm... warmer than the engine compartment. Seems the fan couldn't move enough air to cool the A2W2A system as fast as air alone when you got up to speed.
2nd redesign, and now you have a reservoir in the trunk to keep it away from engine heat, a temp controlled coolant pump, an A2W heat exchanger in the intake path, a W2A heat exchanger in the path of oncoming air, and a temp controlled fan on the W2A exchanger to move air when the vehicle isn't moving. You've got a couple of gallons of coolant, a half mile of 1" or larger hose and pipe, brackets, switches, and relays, and you're going to prove that this system kicks ass. Down the street on a hot day, light to light, engine compartment heats up but the new intercooler system is able to keep IAT's from getting excessive. You get out of town and go for a run and notice that IAT's will drop faster when you're moving than they did with just the fan. Temps don't change quite as fast as with a straight A2A cooler, but they do change. Did you prove the system kicks ass?
Here's the deal: the A2W2A system really turns out to be a slightly sluggish and more complex air to air cooler. Why? Because you're using water to remove heat from air then you're using air to remove heat from water. So you're really using air to remove heat from air and you've added inefficiency by introducing coolant, pumps, fans, and additional heat exchangers. The A2W system shines when you're making short runs and you can stop to exchange your coolant when it gets warm. In this case you can "remove" most of the heat in the coolant by replacing it with something colder. This makes A2W an awesome system at a track. But A2W systems are nowhere near as popular with guys running road races because they only delay temperature changes in the intake air. If IAT is warmer than the coolant, you'll be cooling incoming air. But when IAT's are lower than the coolant temp like after a full throttle blast then you'll be heating the incoming air.
If you want to set up a system and try it, go for it. Keep in mind that with heat energy, whatever goes in has to come back out. imo you could probably set up an A2A system with a temp or dashboard activated mister and see just as much improvement with less complexity and less weight. My strategy with my car was to set up as small an A2A cooler as needed in the path of largest airflow and to use thermal barrier coatings to keep underhood heat from transferring to to other parts in the intake path. This helps keep the system from becoming heat saturated, which is bad. If you want to look at some other people's experiences with A2W systems look for syty.net and search the archives to find what the Syclone guys have tried with their OE equipped A2W2A systems.
hth
-->Slow
great stuff as always..
slowolej wrote:Here's the deal: the A2W2A system really turns out to be a slightly sluggish and more complex air to air cooler. Why? Because you're using water to remove heat from air then you're using air to remove heat from water. So you're really using air to remove heat from air and you've added inefficiency by introducing coolant, pumps, fans, and additional heat exchangers. The A2W system shines when you're making short runs and you can stop to exchange your coolant when it gets warm. In this case you can "remove" most of the heat in the coolant by replacing it with something colder. This makes A2W an awesome system at a track. But A2W systems are nowhere near as popular with guys running road races because they only delay temperature changes in the intake air. If IAT is warmer than the coolant, you'll be cooling incoming air. But when IAT's are lower than the coolant temp like after a full throttle blast then you'll be heating the incoming air.
Very well put, the air-water systems are not good for road racing apps. In that article though, it touches on daily driving the setup, and how you heat up the incoming air once you get out of boost. This helps cool the coolant when you don't need cold air, and this heated air at no (or low) loads I believe would actually help with fuel efficiency, right?
For drag racing apps, as said, the system should not have a water-air exchanger, just the air-water, and the coolant is changed between runs. I have actually seen people buy two duplicate air-air intercoolers, and enclose one with extra sheeting to hold an ice bath which consumes the IC. Get to the strip, swap on the a/w, fill it up, make a run, empty and re-fill, make another run, swap the air-air back on, drive home.
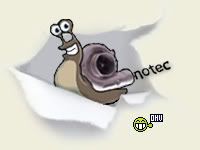
fortune cookie say:
better a delay than a disaster.
Quote:
This helps cool the coolant when you don't need cold air, and this heated air at no (or low) loads I believe would actually help with fuel efficiency, right?
My feeling is that it will may help in some specific situations, but it has a very negative effect of carrying heat from the cooler to other parts of the intake system.
If you could come up with a coolant system in which the coolant changes phase from liquid to gas when heated by intake charge and changes back to liquid at the opposite end without additional mechanical help from a compressor, you'd see large gains. Even with a compressor you might see an advantage if done orrectly. The old discussion aurrounding the a/c system as an intercooler has never (imo) taken into account the sizing of the a/c system. Vehicle a/c systems are massive, sized to cool a hot interior in a very short time. And it's commonly driven by the crank, drawing power roughly proportional to the rpm. Using an electric compressor with thermostatic control, keeping intake air at about 60 deg, and sizing the system appropriately for the heat introduced at maximum boost might provide substantial increases in power for a fixed small cost. At the very least a small refrigeration system which can be activated in times of high intake temps as a supplement might not be a bad idea. Hmmm.
-->Slow
slowolej wrote:If you could come up with a coolant system in which the coolant changes phase from liquid to gas when heated by intake charge and changes back to liquid at the opposite end without additional mechanical help from a compressor, you'd see large gains.
This would require VERY high temps from the compressor, or a vacuum pump of some sort. You wouldn't be able to aid with engine vacuum since it will be under boost, and temps that high from the compressor may be too much to actually cool. However, using an undersized compressor, and a saturated-vapor exchanger should allow for a good milage increase in conjunction.
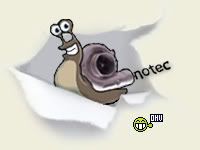
fortune cookie say:
better a delay than a disaster.
Quote:
This would require VERY high temps from the compressor
Lighter alcohols and ammonia are two possibilities which don't require extremely high temperatures.. Water might even work in mild weather. Ammonia is / was used in refrigeration for years, especially in compressor-less applications. Supplemental heat can be drawn from the exhaust, post turbo. Hard to imagine exhaust temps in the downpipe dropping below 300 deg when the system is under load, let's put more of that wasted energy to work. You might have some issues getting the cat converter to light, but your exhaust gasses will have an easier time exiting through smaller pipes if the temp is lower. To really gauge viability I'd need to look at boiling points for a few liquids. Ethyl alchohol boils at roughly 190F.
Quote:
However, using an undersized compressor, and a saturated-vapor exchanger should allow for a good milage increase in conjunction.
This is the type of system I had in mind when I mentioned this. A compressor system is not subject to the effects of gravity in the same way as a purely convective system. And it can provide constant, steady temperature reduction. Sizing the system a little small and playing around with thermal mass to provide a heat sink for times when heat input is on the high side could work in many street cars which see light to mild performance use. Come to think of it, it would be kind of funny sitting in line for the staging lanes on a hot day running the car when everyone else is letting theirs cool, and watching your times drop the longer it runs. Hot oil, warm coolant, and cool intake air would produce nice power gains.
You know, I'm going to be thinking about this all day.
-->Slow
Well, after thinking about it, you would have to bleed off the pressure caused during vaporization. As the mixture quality increases, the higher percentage of steam, which has a higher specific volume (about 200,000x), would cause the fluid enclosure to pressurize, which would in turn raise the fluid temperature. This would all but rule out applying a vacuum to the system (would have needed an outrageous amount of vacuum for water/steam though).
Boiling point for pure ammonia is below freezing, so that wouldn't work, I'm not sure what commercial mixes are though.
Alcohols (especially methyl - 151*F) would be a very good idea though, and excessive pressures (caused by excessive heats) could be applied through a check valve against the pressurized charge pipe and used as a secondary cooling/injection system which would be automatically varied dependent on need.
(I'm sure something doesn't check out there, someone please point it out)
here's a good boiling point table:
http://www.engineeringtoolbox.com/boiling-points-fluids-gases-d_155.html
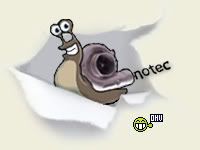
fortune cookie say:
better a delay than a disaster.
So that if im getting it right all thats needed is a condensors, an evaporator, a compressor, lines, valves, and the refridgerant. Danfross makes 12v compressors for boat application ice boxes/ refridgerator applications.
--------------------------------------
04 Cavalier LS Sport- Red with factory silver stripes.
16.186 @ 86.98mph
"Water to air intercooler" - Incorrect terminology. The correct term for a system where water removes the heat only to transfer it to a remote air cooler is... aftercooler. Now back on subject...
My personal idea(never tested), is to build a basic aftercooler setup where pumped water removes heat from the charge-pipe air, then the water runs to a air cooler... only before the water returns to the charge-pipe side, it will also run through an A/C evaporator(of my custom fab work - enclose the evaporator so that water runs through the fins). This obviously requires a modification to the A/C system plumbing and requires you to give up A/C from the vents. There are 6 advantages to this that I can see...
1. The system is cooled by air while cruising so no need for A/C all of the time.
2. When you want to drop temperatures dramatically, turn on the A/C at will(you would do this prior to launching because - IIRC the A/C should shut off @ about 70% WOT anyways).
3. No need to add ice to any reservoir - nor do you even need a reservoir.
4. No need to run coolant lines to the trunk etc.
5. The cooling capatity would be much greater than standard air-to-air intercoolers(which cannot cool below ambient air temps - but this can) or even greater than typical air-water-air aftercoolers. This obviously excludes people spraying their coolers with Nitros Oxide etc etc.
6. Air-Water-Air aftercoolers are much more efficient (less restrictive aka less boost loss) than air-to-air intercoolers. That means less turbo lag and more power.
There is one disadvantage I can see...
1 You might really miss that A/C on those really hot days.
I've never heard of this "part throttle" before. Does it just bolt on?
We call them intercoolers per tradition. A real intercooler is one within a twin turbo or twin charged setup where there is an intermediary cooling method before the next charger. Every "Intercooler" you see is an aftercooler. Therefore:
Bastardking3000 wrote:6. Air-Water-Air aftercoolers are much more efficient (less restrictive aka less boost loss) than air-to-air intercoolers. That means less turbo lag and more power.
(
"Incorrect terminology. The correct term for a system where
ANY FLUID removes the heat from the air after the charger is an aftercooler."
-
"Youth in Asia"...I don't see anything wrong with that.