Alright guys. Who has pics of springs purchased from JBP?
I already have VTLoki's, and PhlatCav's have gone down (although I think they were the same).
Does anybody have their dual springs or their old conical springs?
They said if I got them pictures they could tell me the spring rates
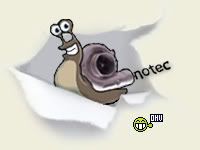
fortune cookie say:
better a delay than a disaster.
You need like up-close pics?
N2O + Bolt-ons
= 220Hp/
250Tq
Coming Soon:HpTunersPro, EagleConnectingRods, WiescoPistons, 13sec2200
MadJack wrote:You mean these?
Well, if you physically have those. They want pictures to ID the springs (since they've used different ones over the years). This way we'll be able to see if someone got screwed over like the "Mantapart" springs, or how useful some of these may actually be...especially those sold for the 2200.
Bballjamal (Cav-AtL) wrote:You need like up-close pics?
I guess close enough that they can tell which they are
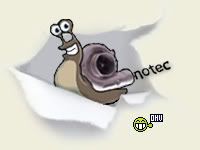
fortune cookie say:
better a delay than a disaster.
I am wondering if anyone has had problems with the first version of the JBP springs? I have the single coil ones from them, and they feel VERY stiff. I fear too stiff, because I had a rocker roller stud pull the threads out of the head, which caused a catastrophic failure in the valve train, and destroyed a piston..
So, anyone else have problems with these? Or know how much stiffer they are? I am afraid to re-use them with my new head and pistons.
Any chance the coils were binding?
-->Slow
Hmm, that could be possible. I can put one back on my old head, but without have it connected to the valve train, i'd have to compress it manually. (i guess I could compress it .450 and see if it binds. I doubt i am getting more lift then that out of the car.
I thought about it some more, but if it was coil bind, it doesn't make sense that only one valve spring was affected. That's not to say that the others wouldn't have pulled out either in time. The threads in the head, for the rocker stud next to the one that failed, also shows signs of coming undone/metal being pulled out.
Another possibility is that the studs were removed at some point, then weren't tightened properly or didn't have threadlocker applied.
Did you have to machine the spring pockets? If so, how much deeper?
-->Slow
I did not machine the spring pockets, and infact, i think they were on a spacer.
I am going to test the coil bind idea tomorrow, and just compress the spring .470 inches. I've calculated that is what my actual valve lift should be. with the cam i have, and the 1.6 rocker rollers. I'll see if it binded at all.
Also, in remembering, i can't be sure if i put thread locker on those studs... so, that may have been it too.
Quote:
I did not machine the spring pockets, and infact, i think they were on a spacer.
Hard to believe those springs won't bind, unless you used taller valves. Just a note: If the spring isn't installed you can't just compress it to .470". You have to compress it to the "installed height" then an additional .470". And you should really compress it (gently) until it binds and measure that amount. That way you know how much clearance you have. You want clearance between the coils even at maximum lift... .060" is the magic number.
-->Slow
slowolej wrote:Quote:
I did not machine the spring pockets, and infact, i think they were on a spacer.
Hard to believe those springs won't bind, unless you used taller valves. Just a note: If the spring isn't installed you can't just compress it to .470". You have to compress it to the "installed height" then an additional .470". And you should really compress it (gently) until it binds and measure that amount. That way you know how much clearance you have. You want clearance between the coils even at maximum lift... .060" is the magic number.
-->Slow
Yup, i do have them installed right now. I was going to compress them installed. I may also remove one, and compress it to the installed height.
Thank you for your opinion slowolej. Perhaps I made the mistake of installing them with the spacer. I will take a few measurements and find out. I obviously don't want this to happen again.
Well, I took a few measurements, and compressed the spring in a vice to the installed height, and then compressed it .5 inches (more then my .47) but wanted to be safe.
It came very close to binding, but was not binding. It is suppose to be close? I have no frame of reference because i don't even have my stock springs anymore. So, i don't know what the stock ones would look like.
My concern is that with the kind of spring pressures at that compressed amount, the threads were torn out. I am definatly not going to run a spacer in the new head, but I am not sure if that is enough to make sure it doesn't happen again. I can assemble the head, and turn the crank to check for binding.
You need .060" which is about as wide as this --> 0
With the springs compressed, can you fit the shim (spacer) between the coils? If not, they were binding.
You can't really use an assembled engine to check for binding if you're using hydraulic lifters. No guarantee the lifters are fully pumped up.
Dan's running ridiculous pressures and he hasn't lost a stud.
-->Slow
Good point on the hydrolic lifters. I'll have to check on the spacer in the coil thing.
Ok, well I looked into the spring binding, and these are the results.
I compressed a spring to install height, and compressed it by 0.47 (my calculated lift)
Long story short is it did not bind, and I had more then .060 inches, but if I calculated in the valve spring seat/spacer, then it would be less then .060
I measured the spacer, which was .035 inches. So, I should be within spec if I do not run a valve spring seat, but my question is, is that safe?
Is the valve spring seat required? The only negative I can see is that if there isn't one, then the spring seat pressure is not evenly distributed over a spacer, but instead directly on where the spring touches the head. This is a smaller area then the spacer obviously. As long as the spring doesn't begin to press into the metal in the head from the pressure, then i'll run it without spacer/valve spring seat. What do you guys think?
Quote:
As long as the spring doesn't begin to press into the metal in the head from the pressure, then i'll run it without spacer/valve spring seat. What do you guys think?
I think this is exactly what can happen. It will depend on how well the springs are located around the guides and in the retainer, and what the pressures are. If the springs have room to "walk" around on the spring seat, you've got the potential for trouble. You might need something like the locators used on the LT4 cyl heads.
-->Slow
Hmm, I'm going to leave a smaller spacer in there .028 inches, and then put the head on the block with no head gasket. I'll then hook up an intake and exhaust valve on a piston with the pushrods, and rocker rollers, pressurized the oil system with a cordless drill ( and keep it going during this experiment). I will then cycle the engine until each valve is open to it's fullest and measure the gap between the coils on the springs, and see how that compares to the measurements i took with the spring outside of the engine.
Ok, well, i ran my experiment, and adjusted the valves quite well. Anyways, i rotated the engine until the valve was at it's lowest point. on the exhaust, that was the one that was close to binding, but had almost twice the .090 required. The intake had tons of room to compress. it didn't open as much as the exhaust, since the cam is meant for a turbo, so it's not as high a lift, but a longer duration. I put the car together, adjusted the valves, started it up, and everything seems to run. I will run it for a day or two, and then take another look at the rockers. i can definitely hear that some of them are a little loose. so, they will need to be tightened. I plan to rotate the engine after each adjusment to make sure the coils don't bind, or come close to binding. I think that will be a safe practice. What do you guys think?