I have taken some measurements that seem "funny" to me. I cant argue with what i observed, so I think my reasoning must be faulty. let me explain.
I wanted to know how much air was actually entering my engine. I purchased a Ford MAF sensor and installed it PRIOR to my supercharger. I then logged the voltage output with my scope as i ran the engine from idle to 7200 RPMs. I found from this test that my engine is intaking 39.8 lbs/min of air. Loosely based off of this number, I was estimating a crank HP of around 398HP. I did not think this was abnormal. In fact this is the measure Ive been calculating all along that i wanted to have, its been my target. But my measured WHP suggest's otherwise. Im making about 230WHP. This is not enough to have 400 on the crank, it would be impossible.
The next thing i did was look at my AFR. I datalogged some WOT pulls, and found my fuel flow and AFR. using these two numbers, I have come to the conclusion that i am only using enough fuel to make 30 lbs/min mix out to 12.8 AFR or about 300 HP at the crankshaft. This is much more inline with the actual WHP im measuring. I have 75 lbs/hr injectors but only using about 50% duty cycle to maintain AFR. I can get more detailed with this if anyone cares, but i dont think its relevant at the moment.
The thing that gets me is, is it possible to injest 40lbs/min of air before the supercharger, and then only have 30 lbs/min of air enter the engine? I know, you might say "its the compressor efficeincy" heating the air up, and lowering the density... True, it sure does... BUT, i also have a humungous intercooler that brings it right back down. In fact, on a day with 75*F ambient temp, my AIT was only 84*F after a WOT pull. So, the final temp gain the air see's before going into my engine is about 10*, and i dont feel that can be the '"problem".
How can this be explained? thanks
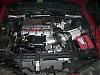
M90'd Built LGO-15 PSI
http://webstarts.com/quadper4mance
in another post , i believe Hahn himself explained to me that CFM's entering a turbo will be the same number that exits the turbo. The turbo will impart mechanical enegy to the CFM's to create the pressure, and it will add heat as a consequence. So, if CFMs' always remain the same, then on my setup, CFMs in should equal out, right? so looking at it from the density stand point, the only that changed was temperature... but again, my FMIC puts that temp right back to where it started. so is it then fair to say that my density remains the same? thats what i think... but apearently thats not how it is. please enlighten me.
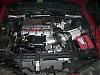
M90'd Built LGO-15 PSI
http://webstarts.com/quadper4mance
Nukkinfuttz wrote:in another post , i believe Hahn himself explained to me that CFM's entering a turbo will be the same number that exits the turbo. The turbo will impart mechanical enegy to the CFM's to create the pressure, and it will add heat as a consequence. So, if CFMs' always remain the same, then on my setup, CFMs in should equal out, right? so looking at it from the density stand point, the only that changed was temperature... but again, my FMIC puts that temp right back to where it started. so is it then fair to say that my density remains the same? thats what i think... but apearently thats not how it is. please enlighten me.
correct. In the process of compressing the air, the supercharger (belt or turbine driven) heats up the incoming air, and the air expands and creates higher pressure. When it goes through the intercooler, the air is cooled and becomes denser (obviously). There are only two places the air can go, either 1) into the engine or 2) back out the compressor inlet. 2 doesn't work because you have already measured the flow rate of air entering the engine. If the air escaped back out , it would then slightly heat the element in the MAF and the MAF would then register a lower flow rate.
You have quite a peculiar problem, though. One thing to note: injectors don't lie. If you are getting 50% dc with 75 lb/min injectors and 12.8 AFR, I calculated it to be 32 lbs/min of air flow.
I know this is something you already know Shawn, but this is a reminder if you've forgotten---> Do you have the idle fuel pressure set to 43.5 psi, or do you have WOT fuel pressure set to 43.5 psi? This is important, because the rated flow of injectors is for a particular fuel pressure. You increase that pressure and the flow rate changes. If you are running 43.5 at idle, then you could very well be flowing near 400hp worth of fuel and air. If this is the case, the only thing I can think of that would attribute to such a low whp compared to crank power is the supercharger. It's important to remember that the m90 is less efficient than the smaller mp62 due to the larger rotors having significantly higher inertia. However, I'm not so sure 100hp is a reasonable power drain for this size of charger.
The only other thing I can think of, is an issue with the MAF. Are you sure you have the correct voltage biasing for the MAF? Is it 5V, 12V or some other value?
I have no signiture
The MAF would need to be scaled/calibrated, which it is not.....

P&P Tuning
420.5whp / 359.8wtq
well, i have a stock FPR referanced to preblower vacumm, so i will assume its 43.5 at idle. Then i have a 1:1 FMU and run about 12 PSI. now that you mention that, makes it even worse! lol i forgot all about that fmu, but i dont think it will do that much.
So, am i looking for a 10 lbs/min air leak to atmosphere then?
Im not sure what you mean by calibrating the maf... it came mounted inside its own housing, so the designer knew exactly how big the housing was. I just sent air thru it. I didnt hook this upto my ECU in any way, all i did was give it the appropriate 12vdc and ground, and then hooked its signal output upto my datalogging oscope. the i ran the engine from idle to redline. i got a full sweep, it was linear, so the airflow was not stalling out or anything. i then compaired the voltage output to a MAF FLOW MAP that i found. It said at X voltage i have X airflow. it had internal density correction. I didnt find much reason to doubt the numbers becuase it said i was moving 40lbs/hr
if you look at my pulley ratio of 1.911, when my motor spins 7200RPM's, my blowing is moving at 13764RPMs. At that rate, according to the M90 blower chart, it says i should be intaking about 560 CFM's. If you take 560 and multiply that by .0714 (weight of 1 CuFt at 80*F), then you get 39.9 lbs/min. It all adds up perfectly, i see no reason to question it at all.
but, the AFR wont lie, so i must have 10 Lbs/min of loss somewhere... but i wanted to check with you guys to be sure im looking for a leak, or if this could somehow be an efficency thing.
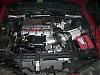
M90'd Built LGO-15 PSI
http://webstarts.com/quadper4mance
MY best theory would be in thermal losses...
Keep in mind that whenever you have energy conversion (of which in a supercharged engine platform there is a lot of) there is a great deal of thermal losses... IE even the most efficient intercooler will not sustain all 12lbs of pressure from the SC across itself...the SC has to make up for it and flow more air to maintain that at the intake valves.
Also did you consider that not all 400hp is going to the crank? Yes the engine is ingesting 400lb/min of air...but is that compensating for the some odd 30% of thermal energy being transferred to the coolant and the exhaust? Not to mention pumping losses?
Just remember, just because your ingesting 400 hp worth of fuel and air does not mean you will see 400hp worth of skedaddle out the crankshaft.. I only Wish IC engines were even close to being that efficient...

Buildin' n' Boostin for 08' - Alex Richards
You say you are running 15PSI, correct? Is that what the charger is limited to with that pulley, or do you have some kind of boost control venting to atmosphere or rerouting back to the intake?
I have no signiture
Also, why do you have a DSM BOV? From the pics of your engine, it looks like you have a draw-through system (charger after throttle body...like most Roots or TS supercharged engines) opposed to a blow-through (charger before throttle...like most centrifugal supercharged engines). Maybe you changed up your setup since, but a BOV is only used in a blow-through system to vent the reflected pressure wave off the throttle to prevent damage to your charger. Maybe that's something you should look at, no?
I have no signiture
Nukkinfuttz wrote:r u drunk?
No, Im just saying that a 10lb/min efficiency loss is perfectly within the realm of possibility when your talking thermal losses in a supercharged IC engine. When it comes to Air and fuel in and Horsepower out there are too many variables to account for to be able to say that X amount of air and fuel = X horsepower.

Buildin' n' Boostin for 08' - Alex Richards
i was running 15 psi a while back, and never changed my sig here. I am currently running 12 psi.
12 psi is the norm for this particular pulley ratio, i do not have any extra means of "boost control", it is what ever it is and im good with that.
Yes, i go TB then SCr the IC then intake mani.
I do have a Blow off valve that is setup in such a way that i beleive it is acting at a bypass vavle. I have removed all the heavy duty springs out of the inside, and left only one very soft spring. I then put what might normally be called the "discharge" and hooked it upto my pressure side of the blower. I then took what is normally the "Pressure side" and hooked it upto the vacumm side of the charger, but after the TB. So, heres how i think its working...
when normal crusing, i have presc'r vacumm on the "hat" of the BOV, and i have the same vacumm signal on the bottom of the poppet vavle and on the pressure side. So, in theory, if all vacumm sources are the same, then it would be biased to the open position becuase of the larger surface area inside of the "hat" that will pull the poppet valve open.
once i hit the gas, the vacumm on the "hat" goes nearer to 1 atmoshere and the spring will take over and close the poppet valve. now, it should be out of "bypass" and all air should be going thru the charger.
Then once in boost, I would be WOT on my TB, so the vacumm signal to the hat would be 1 atmosphere. the spring would hold the poppet valve closed, the boost pressure on the top side of the poppet valve will assist in holding itself closed, and the vacumm signal under the poppet valve (presc'r) will also help hold it closed.
Thats what i think its doing. i could always be wrong. if you see a flaw there, please point it out.
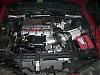
M90'd Built LGO-15 PSI
http://webstarts.com/quadper4mance
Alex Richards wrote:Nukkinfuttz wrote:r u drunk?
No, Im just saying that a 10lb/min efficiency loss is perfectly within the realm of possibility when your talking thermal losses in a supercharged IC engine. When it comes to Air and fuel in and Horsepower out there are too many variables to account for to be able to say that X amount of air and fuel = X horsepower.
Please provide a link to a formula that might explain your point better. There are not too many variable to take into account, people can ballpark it very closely all the time. there is no magic going on, its all precisely calculatable. there are plenty of formulas that say x amount of air and fuel = x hp. its done all the time with fairly accurate precision. I guess you lost me when you said just becuase you put in 400hp worth of air and fuel doesnt mean you will get 400 hp to the crank... well, i must ask then, if you put in that amount of air, and it produced less, then it would no longer be 400 hp worth of air and fuel, it would be some other lesser value, right? its a very circular arguement.
I dont think there is much dispute, that for every 10 lbs/min of airflow an engine has, it should be outputting 100 hp to the crank. maybe 98 maybe 104, but ballparking, 100. no ones gonna argue with that.
or if you take it from a CFM stand point, CFMs' X .65 = HP. that formula comes directly off of a carberator manufacture's website. theres no magic or hupla in there, its pretty straightforward ballparking. simple.
So, all i ask is, if you suggest thermal losses will acount for a 10 lbs/min loss in airflow, could you please provide a link to that info so i may learn it? becuase ive never heard of such a thing before, if its out there, i'd certainly like to know about it.
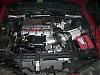
M90'd Built LGO-15 PSI
http://webstarts.com/quadper4mance
Nukkinfuttz wrote:
Please provide a link to a formula that might explain your point better. There are not too many variable to take into account, people can ballpark it very closely all the time. there is no magic going on, its all precisely calculatable. there are plenty of formulas that say x amount of air and fuel = x hp. its done all the time with fairly accurate precision. I guess you lost me when you said just becuase you put in 400hp worth of air and fuel doesnt mean you will get 400 hp to the crank... well, i must ask then, if you put in that amount of air, and it produced less, then it would no longer be 400 hp worth of air and fuel, it would be some other lesser value, right? its a very circular arguement.
I dont think there is much dispute, that for every 10 lbs/min of airflow an engine has, it should be outputting 100 hp to the crank. maybe 98 maybe 104, but ballparking, 100. no ones gonna argue with that.
or if you take it from a CFM stand point, CFMs' X .65 = HP. that formula comes directly off of a carberator manufacture's website. theres no magic or hupla in there, its pretty straightforward ballparking. simple.
So, all i ask is, if you suggest thermal losses will acount for a 10 lbs/min loss in airflow, could you please provide a link to that info so i may learn it? becuase ive never heard of such a thing before, if its out there, i'd certainly like to know about it.
Okay, I was not aware there was no more compensation needed and that was a direct formula...
However, while thinking this over something occurred to me...
Is this formula compensated for humidity? Keep in mind that a MAF measures air mass based on the air's cooling effect on a heated wire... Moisture evaporated in the atmosphere has the same if not better ability to transfer heat away from that wire...I would not be surprised if that 39lb/min number is skewed by moisture content in the air.
Do you have a humidity reading from the day you were doing this?

Buildin' n' Boostin for 08' - Alex Richards
Nukkinfuttz wrote:i was running 15 psi a while back, and never changed my sig here. I am currently running 12 psi.
12 psi is the norm for this particular pulley ratio, i do not have any extra means of "boost control", it is what ever it is and im good with that.
Yes, i go TB then SCr the IC then intake mani.
I do have a Blow off valve that is setup in such a way that i beleive it is acting at a bypass vavle. I have removed all the heavy duty springs out of the inside, and left only one very soft spring. I then put what might normally be called the "discharge" and hooked it upto my pressure side of the blower. I then took what is normally the "Pressure side" and hooked it upto the vacumm side of the charger, but after the TB. So, heres how i think its working...
when normal crusing, i have presc'r vacumm on the "hat" of the BOV, and i have the same vacumm signal on the bottom of the poppet vavle and on the pressure side. So, in theory, if all vacumm sources are the same, then it would be biased to the open position becuase of the larger surface area inside of the "hat" that will pull the poppet valve open.
once i hit the gas, the vacumm on the "hat" goes nearer to 1 atmoshere and the spring will take over and close the poppet valve. now, it should be out of "bypass" and all air should be going thru the charger.
Then once in boost, I would be WOT on my TB, so the vacumm signal to the hat would be 1 atmosphere. the spring would hold the poppet valve closed, the boost pressure on the top side of the poppet valve will assist in holding itself closed, and the vacumm signal under the poppet valve (presc'r) will also help hold it closed.
Thats what i think its doing. i could always be wrong. if you see a flaw there, please point it out.
This seems way to convoluted. You can't avoid the fact that the charger is constantly spinning, so I don't see what kind of gain you could possibly get out of this. You will still be ingesting air through the charger under vacuum, even with the bypass valve. I would maybe try blocking off the BOV and take another reading from the MAF and see what you get.
Alex Richards wrote:Nukkinfuttz wrote:
Please provide a link to a formula that might explain your point better. There are not too many variable to take into account, people can ballpark it very closely all the time. there is no magic going on, its all precisely calculatable. there are plenty of formulas that say x amount of air and fuel = x hp. its done all the time with fairly accurate precision. I guess you lost me when you said just becuase you put in 400hp worth of air and fuel doesnt mean you will get 400 hp to the crank... well, i must ask then, if you put in that amount of air, and it produced less, then it would no longer be 400 hp worth of air and fuel, it would be some other lesser value, right? its a very circular arguement.
I dont think there is much dispute, that for every 10 lbs/min of airflow an engine has, it should be outputting 100 hp to the crank. maybe 98 maybe 104, but ballparking, 100. no ones gonna argue with that.
or if you take it from a CFM stand point, CFMs' X .65 = HP. that formula comes directly off of a carberator manufacture's website. theres no magic or hupla in there, its pretty straightforward ballparking. simple.
So, all i ask is, if you suggest thermal losses will acount for a 10 lbs/min loss in airflow, could you please provide a link to that info so i may learn it? becuase ive never heard of such a thing before, if its out there, i'd certainly like to know about it.
Okay, I was not aware there was no more compensation needed and that was a direct formula...
However, while thinking this over something occurred to me...
Is this formula compensated for humidity? Keep in mind that a MAF measures air mass based on the air's cooling effect on a heated wire... Moisture evaporated in the atmosphere has the same if not better ability to transfer heat away from that wire...I would not be surprised if that 39lb/min number is skewed by moisture content in the air.
Do you have a humidity reading from the day you were doing this?
This is definitely a possibility. Is it pretty humid where you live this time of year?
I have no signiture
Whalesac wrote:Nukkinfuttz wrote:i was running 15 psi a while back, and never changed my sig here. I am currently running 12 psi.
12 psi is the norm for this particular pulley ratio, i do not have any extra means of "boost control", it is what ever it is and im good with that.
Yes, i go TB then SCr the IC then intake mani.
I do have a Blow off valve that is setup in such a way that i beleive it is acting at a bypass vavle. I have removed all the heavy duty springs out of the inside, and left only one very soft spring. I then put what might normally be called the "discharge" and hooked it upto my pressure side of the blower. I then took what is normally the "Pressure side" and hooked it upto the vacumm side of the charger, but after the TB. So, heres how i think its working...
when normal crusing, i have presc'r vacumm on the "hat" of the BOV, and i have the same vacumm signal on the bottom of the poppet vavle and on the pressure side. So, in theory, if all vacumm sources are the same, then it would be biased to the open position becuase of the larger surface area inside of the "hat" that will pull the poppet valve open.
once i hit the gas, the vacumm on the "hat" goes nearer to 1 atmoshere and the spring will take over and close the poppet valve. now, it should be out of "bypass" and all air should be going thru the charger.
Then once in boost, I would be WOT on my TB, so the vacumm signal to the hat would be 1 atmosphere. the spring would hold the poppet valve closed, the boost pressure on the top side of the poppet valve will assist in holding itself closed, and the vacumm signal under the poppet valve (presc'r) will also help hold it closed.
Thats what i think its doing. i could always be wrong. if you see a flaw there, please point it out.
This seems way to convoluted. You can't avoid the fact that the charger is constantly spinning, so I don't see what kind of gain you could possibly get out of this. You will still be ingesting air through the charger under vacuum, even with the bypass valve. I would maybe try blocking off the BOV and take another reading from the MAF and see what you get.
Alex Richards wrote:Nukkinfuttz wrote:
Please provide a link to a formula that might explain your point better. There are not too many variable to take into account, people can ballpark it very closely all the time. there is no magic going on, its all precisely calculatable. there are plenty of formulas that say x amount of air and fuel = x hp. its done all the time with fairly accurate precision. I guess you lost me when you said just becuase you put in 400hp worth of air and fuel doesnt mean you will get 400 hp to the crank... well, i must ask then, if you put in that amount of air, and it produced less, then it would no longer be 400 hp worth of air and fuel, it would be some other lesser value, right? its a very circular arguement.
I dont think there is much dispute, that for every 10 lbs/min of airflow an engine has, it should be outputting 100 hp to the crank. maybe 98 maybe 104, but ballparking, 100. no ones gonna argue with that.
or if you take it from a CFM stand point, CFMs' X .65 = HP. that formula comes directly off of a carberator manufacture's website. theres no magic or hupla in there, its pretty straightforward ballparking. simple.
So, all i ask is, if you suggest thermal losses will acount for a 10 lbs/min loss in airflow, could you please provide a link to that info so i may learn it? becuase ive never heard of such a thing before, if its out there, i'd certainly like to know about it.
Okay, I was not aware there was no more compensation needed and that was a direct formula...
However, while thinking this over something occurred to me...
Is this formula compensated for humidity? Keep in mind that a MAF measures air mass based on the air's cooling effect on a heated wire... Moisture evaporated in the atmosphere has the same if not better ability to transfer heat away from that wire...I would not be surprised if that 39lb/min number is skewed by moisture content in the air.
Do you have a humidity reading from the day you were doing this?
This is definitely a possibility. Is it pretty humid where you live this time of year?
After thinking about this for awhile I remembered something else that also supports this theory...
Keep in mind that modern FI systems in OE vehicles take BARO readings before the engine starts cranking but after the PCM receives power and updates that reading at WOT to compensate the MAF readings for air Density.

Buildin' n' Boostin for 08' - Alex Richards
Quick update: I went on a boost leak quest, and found quite a few little ones...
on each of my intercooler end tanks i drilled and tapped in 1/8" nipples to 1/4 NPT fittings. I leave these capped unless i want to take a reading here. Well, one was completely missing, and the other was so cracked up, it leaked as well.
on the supercharger-to-pipe manifold i made to turn the square outlet of the M90 into a 2.5" pipe, i found three pin holes in the weld. I rewelded those areas to close them up.
on the intake manifold-to-charge pipe adaptor i made, i found another large pin hole. (crappy mig welder). So, i welded that closed as well.
I then found a T-clamp on a charge pipe that was leaking no matter how tight i screwed it. So i removed it and replaced it with a regular hose clamp style. leak fixed.
Thats quite a few leaks. !0lbs/min would equal roughly 140CFMs... which would be about 2.3 cubic feet per second of loss. I dont think these would add up to that number... but then again, im not a airflow expert by any stretch of the imagination, and it very well might be all of it. I guess the next step is to rev it up and see if the boost increases in the manifold.
but that will have to wait till tomarrow, i have to go fishing now. lol
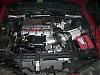
M90'd Built LGO-15 PSI
http://webstarts.com/quadper4mance
Good that you found and took care of boost leaks! Hopefully that should fix most of your problems. Another couple of things though, if it were me, I would ditch the BOV and run a proper bypass valve instead. Also, unlike turbos to a certain extent, superchargers take power to make power, so even though you might have calculations estimating 400 horsepower, a chunk of that is going to be used to spin the supercharger, alternator, ect.
And you gotta remember, no matter the calculations , they aren't an exact science. There are too many other factors such as humidity, ambient temp, IAT's, fuel pressure, even small inconsistencies in engine operation. Show me a PROVEN 100% accurate formula, and ill be amazed.
I would say double check for boost leaks, and then take it to a dyno
Currently #4 in Ecotec Forced Induction horsepower ratings. 505.8 WHP 414WTQ!!!
Currently 3rd quickest Ecotec on the .org - 10.949 @ 131.50 MPH!!!
when you say "proper" bypass valve, i assume you mean a butterfly style throttle plate type thing... trust me, I'd love to, but i cant find one that can be used in a custom application. so, since BOV's where so common and cheap, i figured i'd try to make one of those work. so far it has. At first, i did not have this BOV for a bypass at all. lemme show you what happens if you cruise for about 20 mins with no bypass.... it gets real f'n hot.
but every since ive added this BOV bypass, i can drive for ever and not sieze the blower up. so im pretty certain its works as a bypass becuase i dont have to buy new blowers all the time anymore.
also the take power to make power thing... at my pulley ratio and boost level, this charger steals 45HP from the crankshaft to operate at max RPM and is a linear taper downward to the lower RPMs. BTW, turbos present massive backpressure signals (sometimes upwards of 50-60 PSI) to the engine while operating, so they too take power to make power. there is no such thing as free power. they just are more efficient at the collection of power and require less than a supercharger to move the same amount of air... but they are not doing it free of charge as it sounds like your hinting at.
the talk of humidity, temperature and baro are all completely "taken care of" by using density instead of CFM's. Density is a measure of wieght, and the wieght will be augmented by the affore mentioned things. if they change, so does the density. CFM's however would not change becuase of temp, it would still be just as big, it would just wieght differently. I dont see why its so hard for people to believe that if you have X amount of air, and you mix it to X AFR, that means you will have exactly X amount of fuel "in play", and that amount of fuel is capable of releasing X amount of HP. gasoline has a known energy content per weight... whats so hard about that?
there is no magic.
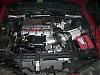
M90'd Built LGO-15 PSI
http://webstarts.com/quadper4mance
Your right, there is no magic, but your theory of X amount of fuel = X amount of horsepower is only true when the air is completely dry. Not to mention your 39lb/min is not compensated for weight, you said that yourself from your first post. Also don;t forget that humidity reduces the weight of the air...not increases because it is displacing the same amount of oxygen as its introducing.
Look at it this way...
30lb/min measured by the MAF at 0% humidity...mixed with X Amount of fuel nets 300hp because we have the right amount of fuel with the right amount of air and our mixture is optimized..
now..
30lb/min measured by the MAF at 100% humidity... mix it with the same amount of fuel will net far less horsepower... Water displaces oxygen...its as simple as that. It's why on a warm nice day typically you will see lower ET's and higher Trap speeds from drag cars and once the temp drops at night (and humidity goes up) those trap speeds drop and ET's go up.
On our Nova we typically dial an entire hundredth slower on a humid day when it gets cold at night.

Buildin' n' Boostin for 08' - Alex Richards
ok. i see what your saying. lets see if we can quantify that then. you say "will net far less HP". Thats a relative statement, and thats the kinda thing im refering to when i say "there is no magic". that statement implies something crazy is happening, but there is no actual quantity.Its as if your saying since this phenomenon is known to occur, we should assume it accounts for all my problems, and i should just stop looking any further for any other problems. that is not fair to say.
"Far Less" to me may not mean the same to you and vise-versa. So, lets see if we can dig up some formulas or realworld examples that suggest exactly how much effect humidity has. I can argue all day long with your statement of "Far Less" becuase it has no specific quantity. lets make it specific via a formula and then I'll have no arguement AND I'll know exactly how much loss it can account for, so i can be on the look-out for the rest. Deal? I'll be looking too and post up if i find something concrete.
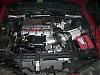
M90'd Built LGO-15 PSI
http://webstarts.com/quadper4mance
Quoted from this source
http://www.chevyhiperformance.com/techarticles/67678_density_altitude_adjustment_reading/index.html
"""Kyle also gave us some interesting insights into the relative strengths of temperature, pressure, and humidity. Temperature has the strongest affect on density altitude with a one-degree change worth a 100-foot change in density altitude. Pressure is next with a 0.01-in/Hg change also worth a 100-foot change in density altitude. Finally, a 10 percent difference in humidity can also affect the density altitude by 100 feet.
Kyle runs both a Super Stock Camaro and a dialed-in 9.90 Super Gas Corvette. According to Kyle, a typical race car like his Super Gasser will lose 0.01-second for every 100 to 120 feet of change in density altitude. This may not be as solid for street cars, but a 500-foot change in density altitude will still be worth as much as 0.03 second. """"
IMHO it seems humidity has a very small effect. definately some measureable effect, but hardly any at all. If this mans car looses 0.01 second for every 100 feet of density altitude change AND a 10 percent change in humidity can affect the density altitude by 100 feet, Or what if you had 100 percent humidity? would that mean a 0.10 second difference? it seems a very very small change to me. im sure this is very important to a bracket racer with money on the line, but its not that big a deal to me or my calculations.
Quoted from these guys who run supersonic bonniville salt flat cars...
http://www.thrustssc.com/thrustssc/Engineering/Atmospheric_effect.html
"""""Humidity does not have a first-order influence on engine or car performance""""
again, humidity has been minimized by a person in the know.
Quoted from this test determining the effects of Temp, Baro and humidiy on engine performance of a 4 cly engine....
http://www.scielo.br/scielo.php?script=sci_arttext&pid=S1678-58782003000300010
""""Air humidity influences the performance of an engine, though not comparable to the influence of pressure and temperature """"
Again, they admit it has some effect, but not even compairable (or in the same boat as ) pressure and temp. they have also minimized the humidity effect.
Or, try messing with this calculator...
http://wahiduddin.net/calc/calc_hp.htm
you can see that going from 10% humidity to 100% humidity will make a difference equal to about 400 feet of altitude change... which i think anyone would agree is not worth mentioning.
I dont see a need to keep going. no body seems to think humidity adds upto much. So, "Net far less HP" is going to amount to almost nothing in my opinion. See what happens when you take the magic out of it?
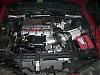
M90'd Built LGO-15 PSI
http://webstarts.com/quadper4mance
You completely missed the original point of the humidity argument. A MAF is a very simple voltage divider comparator. It has one reference voltage and it has the voltage seen by the heated element in the intake stream. You can think of this element as a thermistor if you'd like (cause that's essentially what it is). When you cool this element, you have a potential difference between the reference voltage and the voltage across the element. For a given mass of air, the amount of moisture in it will affect the rate of cooling of the element. You can flow 30lbs/min with 0% humidity and you can flow 30lbs/min with 80% humidity, and you will physically see a difference on your oscilloscope. You need some kind of correction factor to account for this. I personally, don't know what that factor is. It could be linear, logarithmic, exponential, etc. So the reading you took could have the same effect of cooling 40lb/min of air at 0% humidity, when you might actually only be flowing 30lb/min at 90% humidity. You may want to look into that.
Glad to see you found/fixed some leaks. Keep us updated.
I have no signiture
when people say its 50% humidity, that does not mean that per any given volume of air, 50% of it is water. its not even like that. there is a chart that shows at each temperature rating how much water is possible to store in the air. The max possible will be called 100%. when its raining outside, that is 100% humidity! but there is still plenty of air to breath! thats becuase the max possible water content of air is still only 2.7% of its volume at 85*F. so, lets say a regular day with 50% humidity, that water vapor would only account for 1.35% of the entire contents of a given volume.
so, lets take that and apply it to my testing and engine. i intaked roughly 40lbs/min of airflow according to the MAF. if the humidity on that day was 100% (which was not likely, but i'll give you worse case senario) then that means the amount of real oxygen content equivalent would be 97.3% of that original value, since we know the air can only hold upto 2.7% of its volume in water vapor. so, 97.3% of 40 lbs/min would be about 38.92 lbs/min if 100% humidity were present. more than likely not, so ill say it was even more closer to the original 40lbs/min. just like engine performance is hardly effected, why would it change anything here so drastically as 25% of my airflow going missing due to humidity? dude... seriously. humidity means nothing. i dont think 2.7% of the medium im measuring could throw the reading off by 25 %. that does not sound credible. i wont deny it may do something... but not 1/4 of the signal.
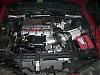
M90'd Built LGO-15 PSI
http://webstarts.com/quadper4mance
sigh...You didn't read a word I said.
Moisture affects the rate of cooling. This has nothing to do with water displacing air. My argument is that you could be reading a higher potential difference from the voltage readings of the MAF due to the humidity cooling the heated element more than on a low humidity day. That is, if you assumed 0% humidity for the voltage scaling, then you aren't measuring the true mass flow rate. Sensors only work in as much as we understand the properties of the world around us, and without the support of other sensors, some sensor readings are mere shots in the dark. For example, how can you accurately expect to run an engine with a speed density tune well in various climates if you don't have an IAT/MAT?
I have no signiture